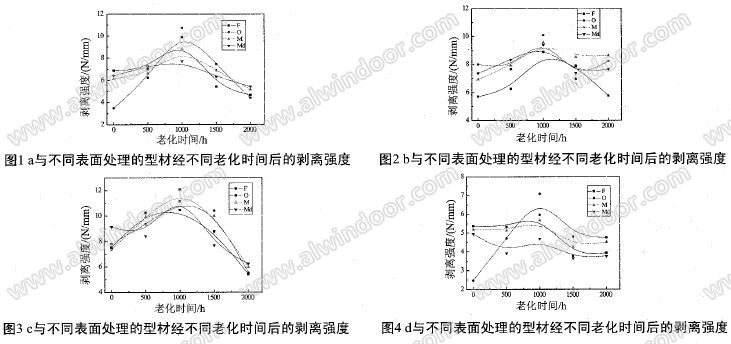

其老化机理可能是因为硅酮结构密封胶
固化后同时受水和热的影响。水有两方面的作用:其一使硅酮结构密封胶进一步交联,分子链逐渐加长,分子间内聚力增加,从而使强度增加;其二则使其发生水解而降解,导致强度降低。热的作用在短时间内会加快自由基反应的交联过程,使强度增加,但长期的热作用反而会促使胶的老化,使强度下降。从而使得单组分硅酮结构密封胶在55℃热水下,剥离强度先增加,随后随时间的延长而下降。
对于四种双组分试样,标态时,A、B、D与氟碳喷涂的铝型材不涂底漆时(底漆只用在粉末喷涂上)粘结较差,B、D与阳极氧化的铝型材不涂底漆时粘结较差,D与粉末喷涂的铝型材涂底漆后粘结较差。对于老化后的试样,D与氟碳喷涂的铝型材不涂底漆时粘结较差,A、C与阳极氧化和粉末喷涂的铝型材粘结较差。对于与粉末喷涂的铝型材粘结后的双组分试样,涂底漆后,A的剥离破坏面积由100%下降为30%,剥离强度有较大提高,其余试样影响较小。
对于随老化时间影响较小的双组分硅酮结构密封胶,表明在养护期间,两种组分可能已基本完全反应,链段已充分交联,在55℃热水下老化时,水解和热作用同时进行,降解和交联的竞争大致相当,使得剥离强度变化幅度较小。当降解大于交联时,剥离强度下降。对于标态时与型材表面粘结较差,经热水老化后反而粘结性能提高的现象,可能是因为,不同表面处理的铝型材因表面处理的方式不一样,涂层成分不一样造成胶与型材界面粘结不充分,随着老化的进行,短期的热水作用促进了界面各组分的交联,从而使得剥离强度提高。
2.2 90℃热水下不同表面处理的铝型材对单、双组分硅酮结构密封胶长期粘结性的影响与55℃热水老化相比较,9O℃热水老化条件苛刻,大部分结构胶密封胶本体己变软、变黏。从表3可知,b90℃热水下老化条件下对多种表面粘结性最优,其他胶对M及Md表面均100%粘结破坏;90℃热水下老化0表面的粘结稳定性最优;F次之。90℃热水老化后各样品粘结破坏强度见表4。

由表4可知,90℃热水老化条件下b对多种表面处理型材的剥离强度最大,粘结性最优;其余粘结稳定性均较差。在三种表面处理的型材中,M/Md表面粘结后耐90~C热水条件下老化最差。所有的双组分样品均表现为较低的剥离强度,其性能大幅下降直至失去使用价值, 因此对硅酮结构密封胶的选择必须慎重。
3 结论
(1)F表面与多种胶常温粘结欠佳,但热水处理1500h内改善;O表面与多种胶常温粘结欠佳,但热水处理1000 h内改善;M表面与多种胶常温粘结良好。Md的平均粘结破坏面积最小,表明涂底漆后粘结稳定性提高,表面粘结稳定性优。
(2)对于55℃单组分样品,随着老化时间的延长,基本上1000 h时各试样剥离强度最高;随后随着时问的延长,达到2000h时,强度普遍下降。双组分样品的强度普遍低于同条件下的单组分样品,且热水对其的老化影响要小于单组分样品。
(3)在90℃高温下,样品与氟碳喷涂和阳极氧化表面处理的铝型材的粘结性能要优于与粉末喷涂的铝型材。粉末喷涂的铝型材由于涂层在高温下与型材的附着力已失效,除b夕l,其余样品均表现为完全界面破坏。【完】
上一页12下一页